QR-kód
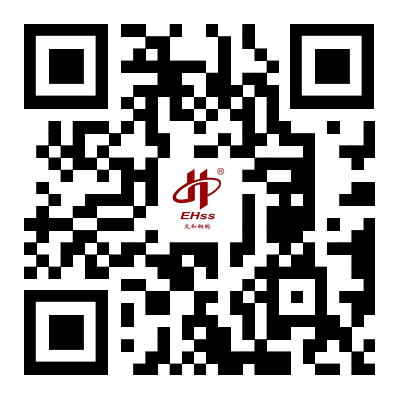
Termékek
Lépjen kapcsolatba velünk
Telefon
Email
Cím
No. 568, Yanqing First Class Road, Jimo High-Tech Zone, Qingdao City, Shandong tartomány, Kína
Acélszerkezetű gépészeti épületszázad zöld projektjeként ismert, az acélszerkezetnek számos előnye van, mint például a nagy szilárdság, az erős terhelhetőség, a könnyű súly, a kis helyfoglalás, az alkatrészek egyszerű gyártása és beszerelése, a fa megtakarítása stb. egyre szélesebb körben alkalmazzák az ipari és polgári épületekben.Acélvázas épületek és acélszerkezetű raktárak mindenhol megtalálhatók.
Az ipar gyors fejlődésével az acél korrózióállósága és a rozsdával, korrózióval és egyéb problémákkal szembeni gyenge ellenállás fokozatosan megjelent, különösen a tengerparti területeken, és a vegyipar kiemelt problémává vált!
Az acélszerkezetek korróziója nemcsak gazdasági veszteséget okoz, hanem rejtett veszélyt is jelent a szerkezet biztonságára, gyakoriak az acélkorrózió okozta mérnöki balesetek, így az acélszerkezetek (különösen a vékonyfalú acélelemek) korróziógátló kezelése nagy gazdasági és társadalmi jelentőségű, és az alábbiakban bemutatunk néhány bevezetőt és megbeszélést az építési folyamat során felmerülő problémákról és egyes kezelési módszerekről.
1. Az acélszerkezetek korróziójának fő okai
Az acélkorrózió megelőzése az acélkorrózió okainak megértésével kezdődik.
1.1 Acél korróziós mechanizmusa szobahőmérsékleten (100°C alatt)
Az acél szobahőmérsékleten történő korróziója főként elektrokémiai korrózió. Az acélszerkezeteket szobahőmérsékleten használják a légkörben, és az acél a nedvesség, oxigén és egyéb szennyező anyagok (tisztítatlan hegesztési salak, rozsdaréteg, felületi szennyeződés) hatására korrodálódik a légkörben. A légkör relatív páratartalma 60% alatti, az acél korróziója nagyon csekély; de amikor a relatív páratartalom egy bizonyos értékre emelkedik, az acél korróziós sebessége hirtelen megemelkedik, és ezt az értéket nevezzük kritikus páratartalomnak. Szobahőmérsékleten, az általános acél kritikus páratartalom 60% és 70%.
Ha a part menti területeken a levegő szennyezett vagy sós a levegő, a kritikus páratartalom nagyon alacsony, az acélfelület könnyen vízréteget képez. Ebben az időben a hegesztési salak és a kezeletlen rozsdaréteg (vas-oxid) a katód, az acél szerkezeti komponensek (alapanyag) anódként a vízfilmben elektrokémiai korrózió. Az acélfelületen adszorbeált légköri nedvesség vízfilmet képezve az acél korróziójának meghatározó tényezője; a légkör relatív páratartalma és a szennyezőanyag-tartalom a légköri korrózió mértékét befolyásoló fontos tényezők.
1.2 Acél korróziós mechanizmusa magas hőmérsékleten (100 ℃ felett)
Az acél korróziója magas hőmérsékleten főként kémiai korrózió. Magas hőmérsékleten a víz gáz halmazállapotban létezik, az elektrokémiai hatás nagyon kicsi, másodlagos tényezővé redukálódik. Fém és száraz gáz (például O2, H2S, SO2, Cl2, stb.) érintkezés, a megfelelő vegyületek (kloridok, szulfidok, oxidok) felületképzése, az acél kémiai korróziójának kialakulása.
2 Acélszerkezetek korrózió elleni védekezésének módszerei
Az acélkorrózió elektrokémiai elve szerint mindaddig, amíg a korróziós akkumulátor kialakulását megakadályozzák vagy megsemmisítik, vagy a katódos és anódos folyamatokat erősen blokkolják, az acél korróziója megelőzhető. A védőréteg módszer alkalmazása az acélszerkezet korróziójának megelőzésére jelenleg elterjedt módszer, az általánosan használt védőréteg a következő fajtákkal rendelkezik:
2.1 Fém védőréteg: a fém védőréteg katódos vagy anódos védőhatással rendelkező fém vagy ötvözet, galvanizálással, szórással, vegyi bevonattal, melegítéssel és szivárgó bevonattal és egyéb módszerekkel, a fémfelület védelmének szükségessége fém védőréteg (film) kialakítása érdekében a fém izolálása a korrozív közegtől a korrozív közeggel érintkezve, vagy a fémvédelem elektrokémiai védőhatásának alkalmazása a korrózió megelőzése érdekében.
2.2 Védőréteg: kémiai vagy elektrokémiai módszerekkel az acél felületének korrózióálló vegyületfilm előállítására, a korrozív közeg és a fém érintkezésének elkülönítésére, a fémek korróziójának megakadályozására.
2.3 Nem fémes védőréteg: festékekkel, műanyagokkal, zománccal és más anyagokkal, festéssel, szórással és egyéb módszerekkel, védőfóliát képez a fém felületén, hogy a fém és a korrozív közeg elszigetelje, és megakadályozza a fém korrózióját .
3. Acél felületkezelés
A gyárba történő acélfeldolgozás előtt az alkatrészek felülete elkerülhetetlenül foltos lesz olajtól, nedvességtől, portól és egyéb szennyező anyagoktól, valamint sorja, vas-oxid, rozsdaréteg és egyéb felületi hibák. Az acélszerkezetek korróziójának korábbi főbb okaiból tudjuk, hogy a szennyezőanyag-tartalom a légköri korrózió mértékét befolyásoló fontos tényező, a felületi szennyeződések pedig súlyosan befolyásolják a bevonatok tapadását az acél felületén, és a festéket. a korrózió alatti film tovább tágul, ami a bevonat meghibásodását vagy károsodását eredményezi, és nem tudja elérni a kívánt védőhatást. Ezért az acél felületkezelésének minősége a bevonat védőhatására és a hatás élettartamára, esetenként még jobban, mint maga a bevonat, a teljesítménybeli különbségek változatosságát a következő szempontok hatásában kell hangsúlyozni:
3.1. Azoknál a teherhordó alkatrészeknél, amelyek a szervizelés során nehezen javíthatók, a vízkőmentesítési fokozatot megfelelően növelni kell.
3.2. A vízkőmentesítés előtt és után gondosan el kell távolítani a zsírt, a sorját, a gyógyszer bőrét, a fröccsenést és a vas-oxidot.
3.3. a vízkőmentesítési és festési munkák minőségi átvétele az előírásoknak megfelelő legyen.
4. Korróziógátló bevonat
A korróziógátló bevonatok általában alapozóból és fedőbevonatból állnak. Alapozó a porban több, kevesebb alapanyag, film durva, az alapozó feladata, hogy a festékfilmet alulról és a fedőréteg kombinációjával szilárd, azaz jó tapadásúvá tegye; Az alapozó korróziógátló pigmenteket tartalmaz, megakadályozhatja a korrózió kialakulását, és néhány lehet a fém passziválása és az elektrokémiai védelem, amely megakadályozza a fém rozsdásodását. A fedőbevonat kevésbé por, több alapanyag, miután a fólia fényes, a fő funkciója az alapozó alsó rétegének védelme, tehát légköri és nedvességálló legyen, és ellenálljon a fizikai és kémiai lebomlásnak. időjárás okozta. A jelenlegi trend a műgyanták használata a közeg időjárásállóságának javítására. Az atmoszférikus ellenállással rendelkező korróziógátló bevonatok általában csak a légköri gőzfázisú korróziónak ellenállnak. Savak, lúgok és egyéb közegek által korróziónak kitett helyeken sav- és lúgálló bevonatokat kell használni.
A védő funkció szerint a korróziógátló festék alapozóra, középső festékre és fedőrétegre osztható, minden festékrétegnek megvannak a maga sajátosságai, mindegyik felelős a saját felelősségéért, a rétegek kombinálásáért, a kompozit bevonat kialakításáért. javítja a korróziógátló teljesítményt, meghosszabbítja az élettartamot.
4.1 alapozók
Az alapozóréteg leggyakrabban használt korróziógátló bevonatok cinkben gazdag alapozó és epoxi vasvörös alapozó, a cinkben gazdag festék nagyszámú mikrofinom cinkporból és kis mennyiségű filmképző anyagból áll. A cink elektrokémiai tulajdonságai magasabbak, mint az acélé, és korróziónak kitéve "önfeláldozó" hatást fejt ki, így az acél védett. A cink-oxid korróziós termék kitölti a pórusokat, és sűrűbbé teszi a bevonatot. Az általánosan használt cinkben gazdag alapozónak a következő három fajtája van:
(1) vízüveg szervetlen, cinkben gazdag alapozó, alapanyagként vízüveg, cinkpor hozzáadása, keverés és ecsettel, kikeményedés után vízzel öblítendő, az építési folyamat összetett, kemény folyamatkörülmények, a felületkezelésnek kötelező legyen az Sa2,5 vagy több, amellett, hogy a környezeti hőmérséklet, a páratartalom követelményei, a bevonó film kialakulása könnyen repedezhető, hámló, és ritkán használt.
(2) oldható szervetlen cinkben gazdag alapozó, az alapozó etil-ortoszilikáton, oldószerként alkoholon, részben hidrolizált polimerizáción alapul, cinkporral keverve egyenletesen bevont filmet.
(3) cinkben gazdag alapozó, ez epoxigyanta filmképző alapanyagként, cinkpor hozzáadásával, kikeményítéssel bevonat kialakításához. Az epoxi cinkben gazdag alapozó nem csak kiváló korróziógátló tulajdonságokkal és erős tapadóképességgel rendelkezik, és a következő bevonattal az epoxi vas-felhőfesték is jó tapadású. Főleg az acélvázszerkezet általános légkörében és a petrolkémiai berendezések korróziójában használják.
Az epoxi vas-oxid vörös alapozó kétkomponensű festékdobozokra van felosztva, az A komponens (festék) epoxigyantából, vörös vas-oxid és egyéb rozsdagátló pigmentek keményítő, süllyedésgátló stb., B komponens térhálósító, a bevetés arányának felépítése. A vas-oxid vörös egyfajta fizikai rozsdagátló pigment, természete stabil, erős fedőképesség, finom részecskék, jó árnyékoló hatást fejthet ki a festékfilmben, jó rozsdagátló tulajdonságokkal rendelkezik. Az epoxi vas-oxid vörös alapozó az acéllemezen és az epoxifesték felső rétege jó tapadású, szobahőmérsékleten gyorsan szárad, a felületi festék felső rétege nem vérzik el, gyakrabban használják acél csővezetékekben, tartályokban, acélszerkezetek korróziógátló projektjeiben , rozsda alapozóként.
4.2 középső festékréteg
A középső réteg festék általában epoxi csillám és epoxiüveg festék vagy epoxi vastag hígtrágya festék. Az epoxi csillámfesték alapanyagként epoxigyantából csillámvas-oxid hozzáadásával készül, a csillám-vas-oxid mikroszerkezete olyan, mint a pelyhes csillám, vastagsága mindössze néhány mikrométer, átmérője több tíz-száz mikrométer. Magas hőmérséklet-ellenálló, lúgálló, saválló, nem mérgező, a pelyhes szerkezet megakadályozhatja a közeg behatolását, javítja a korróziógátló teljesítményt, és alacsony zsugorodás, felületi érdesség, kiváló korróziógátló festék középső rétege. Az epoxi üvegkőfesték alapanyagként epoxigyanta, adalékanyagként pelyhes üvegréteggel, valamint számos vastag lapátos korróziógátló festékből álló adalékanyaggal. Az üvegréteg vastagsága mindössze 2-5 mikron. Mivel a pikkelyek a bevonatban fent és lent rétegekben helyezkednek el, egyedi árnyékoló szerkezet alakul ki.
4.3 fedőlakk
A fedőbevonatokhoz használt festékek árfekvésük szerint három kategóriába sorolhatók:
(1) A szokásos minőségű epoxi festék, klórozott gumi festék, klórszulfonált polietilén és így tovább;
(2) A közepes minőségű poliuretán festék;
(3) A magasabb minőségű szilikonnal módosított poliuretán festék, szilikonnal módosított akril fedőbevonat, fluorfesték és így tovább.
Epoxi festék kémiai kikeményedés után, kémiai stabilitás, sűrű bevonat, erős tapadás, magas mechanikai tulajdonságok, ellenáll a savnak, lúgnak, sónak, ellenáll a különféle kémiai közegek korróziójának.
5. A korróziógátló festék kiválasztásánál több szempontot is figyelembe kell venni
5.1 Figyelembe kell venni a szerkezet használati feltételeinek és a kiválasztott festékválasztéknak a konzisztenciáját, a korrozív közeg (típus, hőmérséklet és koncentráció) gázfázis vagy folyadékfázis, forró és nedves területek vagy száraz területek és egyéb tényezők alapján. kiválasztási feltételek. Savas közeghez a jobb savállóságú fenolgyanta festék, míg lúgos közeghez a jobb lúgállóságú epoxigyanta festéket érdemes használni.
5.2 Figyelembe kell venni az építési feltételek lehetőségeit. Van, amelyik ecsetelésre, van, amelyik permetezésre alkalmas, van, amelyik természetes szárításra alkalmas filmréteg kialakítására és így tovább. Általános körülmények között száraz, könnyen permetezhető hidegen kötő festéket célszerű használni.
5.3 Fontolja meg a bevonatok megfelelő illeszkedését. Mivel a festék nagy része szerves kolloid anyag, mint alapanyag, minden fóliaréteget fessen be, elkerülhetetlenül sok kivételesen kis mikroporózus, korrozív közeg még mindig áthatolhat az acél erózióján. Ezért a jelenlegi festék felépítése nem egyrétegű, hanem többrétegű bevonatú, a cél a mikropórusos minimálisra csökkentése. Az alapozó és a fedőlakk között jó alkalmazkodóképességnek kell lennie. Ilyen például a vinil-klorid festék és foszfátozó alapozó vagy vasvörös alkid alapozó, amely támogatja a jó eredmény használatát, és nem használható a felhasználást támogató olaj alapú alapozóval (például olaj alapú vörös festékkel). Mivel a perklór-etilén festék erős oldószereket tartalmaz, tönkreteszi az alapozó filmet.
Nagyon fontos, hogy jó munkát végezzünk a rozsda- és korrózióvédelem területén az acélszerkezetű épületek fejlesztésének elősegítése, az anyagok megtakarítása, az épület élettartamának meghosszabbítása, a biztonságos gyártás biztosítása és a környezetszennyezés csökkentése érdekében.
No. 568, Yanqing First Class Road, Jimo High-Tech Zone, Qingdao City, Shandong tartomány, Kína
Copyright © 2024 Qingdao EIHE Steel Structure Group Co., Ltd. Minden jog fenntartva.
Links | Sitemap | RSS | XML | Privacy Policy |
Teams